Integrating new automation? Here are the keys to success in plastics manufacturing
Effective project management and standard robots are key to smooth automation in plastics manufacturing. Our expertise ensures seamless installations and future-proof solutions.
Integrating new automation systems can be a complex and challenging process, especially for plastics manufacturers. The introduction of robotic automation into an existing or new production line often involves a lot of moving parts. With our extensive background in automation for the plastics industry, we’re breaking down two keys to ensure smooth and successful installation of new robotic automation systems in plastics manufacturing.
Key #1 - Good project management, smooth integration
Good automation integration is good project management. This is particularly crucial when introducing new machinery, molds, and automation simultaneously. Each of these components comes from different suppliers – the machine supplier, mold supplier, and automation supplier – all of whom need to work in unison to achieve a seamless installation.
A lot of problems with automation integration occur from challenges associated with extracting the part from the mold. This is why automation integrators need to be up to date on all aspects of mold from design to functionality. For instance, insert molding, molds without ejectors, or the need to remove runners require a higher level of engineering expertise for a robot to operate smoothly. These processes are much more demanding compared to simpler operations where parts come out of the mold without any additional degating, heat treatment, or finishing. For automation integrators, any uncertainties in how the mold functions is sure to create headaches in the future – both for the manufacturer and the integrator.
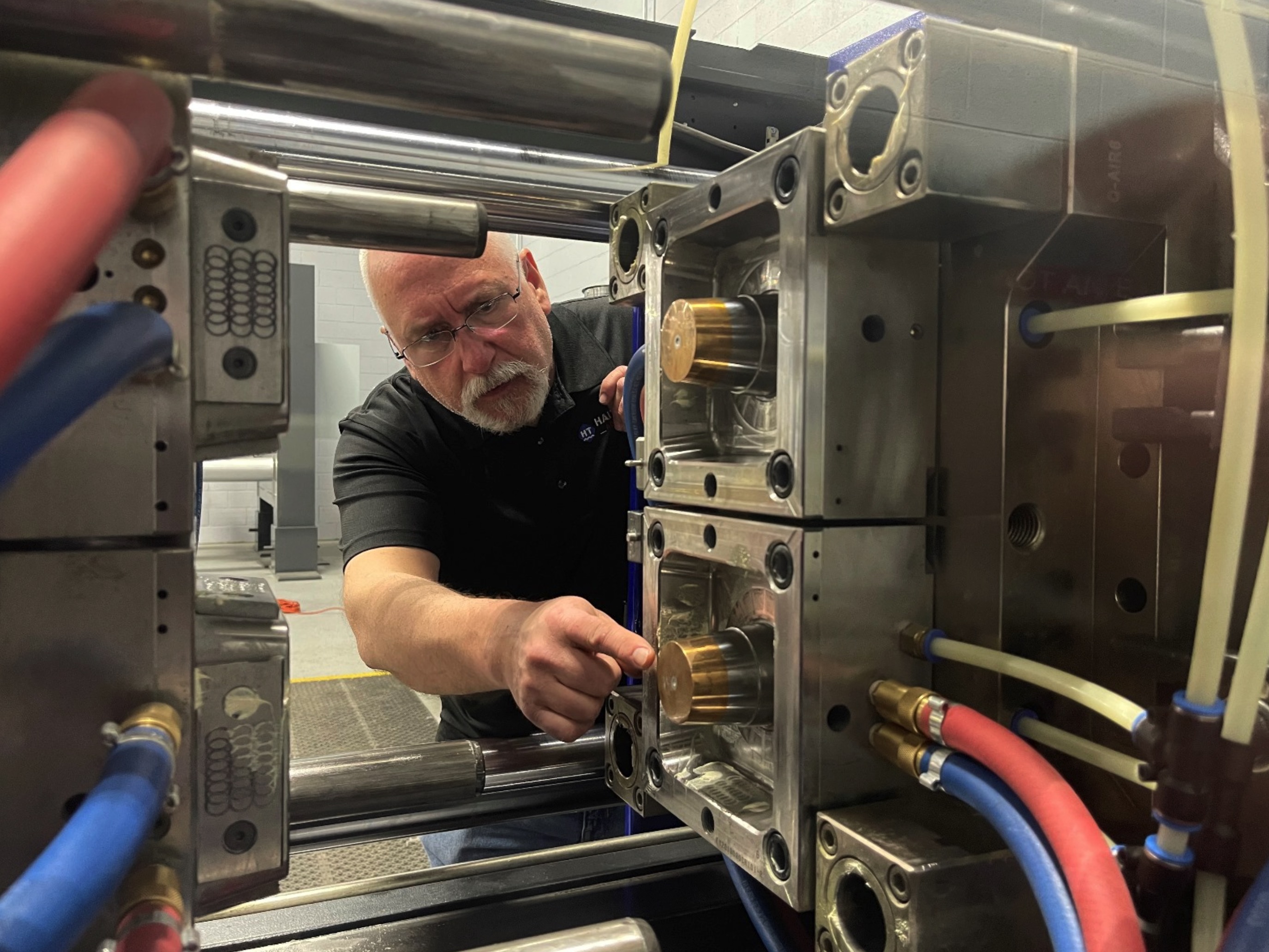
We’ve learned from over 1000 robot installations in North America and provide all our customers with a dedicated project manager from inception through installation. Each dedicated project manager has been through the entire automation integration process many times, provides customers with a weekly update on the status of the project, and ensures that all items are checked off our list to ensure that installation and startup are smooth. This includes everything from gathering the drawings of the mold to an IMM site survey to a full data package of mold, part, and insert drawings. This ensures that …
Key #2 - When possible, shift towards standard robots
Historically, the plastics manufacturing industry relied heavily on custom-built robotic automation. However, there has been a noticeable shift towards the use of standard robots, and for good reason.
Standard robots offer a level of flexibility and future-proofing that custom-built robots simply cannot match. When a manufacturer moves away from a specific application, custom-built robots often become obsolete and are discarded. In contrast, standard robots can be repurposed for a variety of applications, providing a better return on investment.
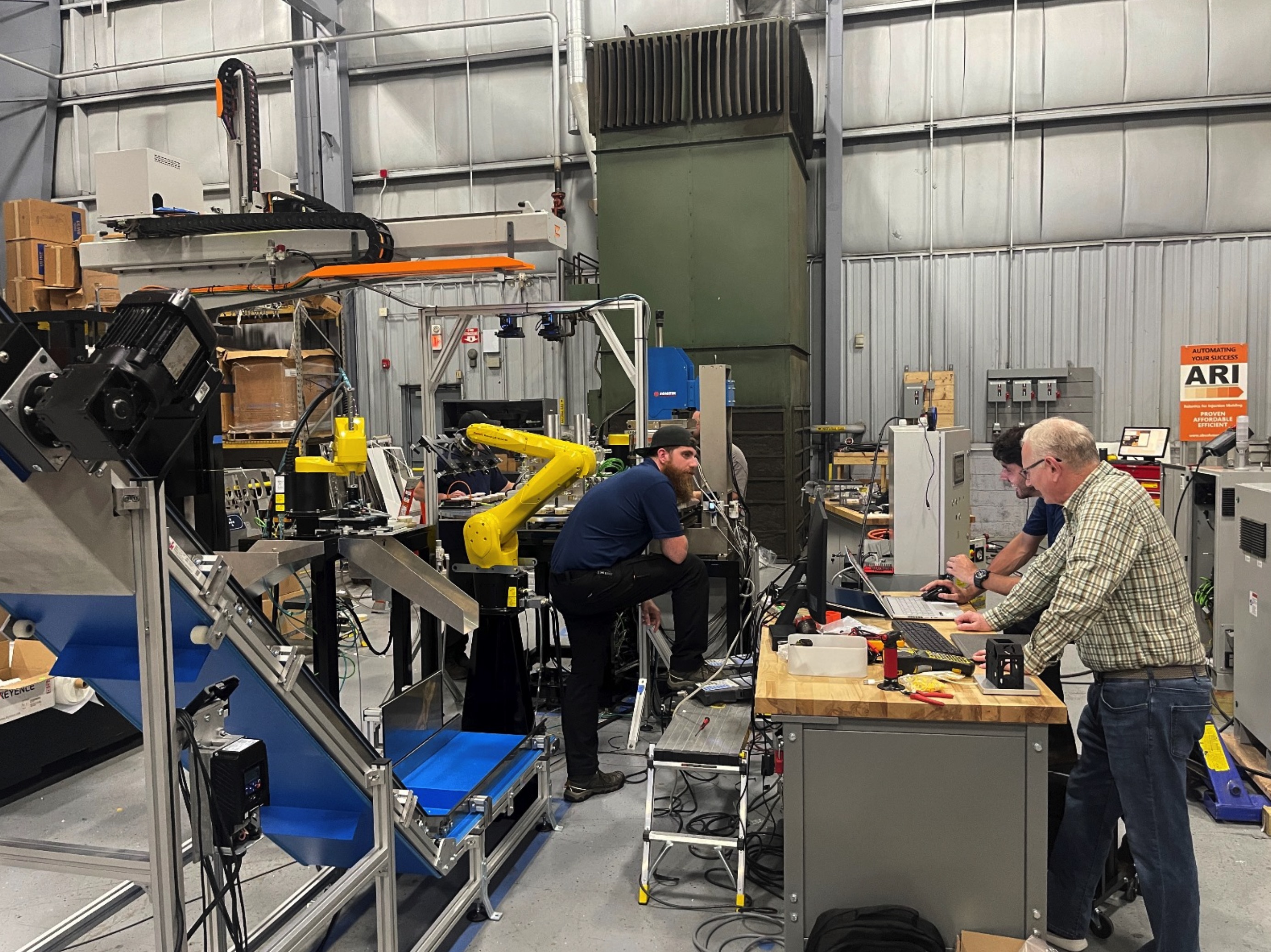
Moreover, custom-built automation systems are prone to unexpected issues and complications. Integrators with experience in standard robots have typically encountered and resolved most common integration challenges, reducing the likelihood of unforeseen problems. This accumulated knowledge and experience of over 1200 installs streamline the integration process, making it more predictable and manageable. Based on cavitation, cycle time, and desired downstream automation, we can almost always know whether a more versatile FANUC or a more economical top-entry 3- or 5-axis robot.
Of course, there may always be a real need for custom-built automation. We work on many custom automation applications in plastics as a Certified FANUC Integrator. In these cases, our first key to smooth automation projects becomes even more paramount – machinery, mold, and automation need to have tight communication loops on all the technical specifics.
Whether it’s a first time or the 100th, there’s bound to be something that goes bump in the night with the implementation of new machinery, molds, and automation. That’s why the smoothest projects across machine, mold, and automation suppliers will always be determined by good communication and efficient project management. If you’re in the process of spec-ing a new automation project, reach out to us to hear more about how our dedicated project managers help ensure smooth installations and startups. They’re professionals at keeping track of all of the often overlooked, little things that can slow down a project.