FANUC Authorized System Integrator
We are a FANUC Authorized System Integrator, with the capability to automate a single machine or your entire facility. Our dedicated team of engineers is with you every step of the way, from quoting to aftermarket support. At ARI we believe consistent communication and status updates over the lifetime of the project ensures an on time and on budget installation.
- Ties seamlessly into the molding machines
- Very large payload capacity
- Complex downstream capabilities
- Cycle tracking and data reporting
- Multiple mounting locations (top, side, floor, etc.)
- High precision insert capabilities
- Can be used in multiple molding machine configurations
- High-speed cycle saving movements
For 6-axis automation solutions, we are certified integrators of FANUC robots. FANUC robots are more than capable to meet your automation needs for complex or large applications.
- Versatile and flexible for multi-function downstream requirements
- Large payload capabilities
- Multiple different take-out methods
FILTER:
ARI Conveyors
ARI’s conveyors are engineered to increase productivity without going over budget. Easy to assemble and operate, these conveyors are shipped directly from Absolute’s facility in Worcester, MA. Conveyors have standard variable drives with indexing capabilities and they are fully supported by the Absolute Group of Companies. If you have any questions or would like to request a quote please give us a call at 508-792-4305 or email us at sales@absoluterobot.com
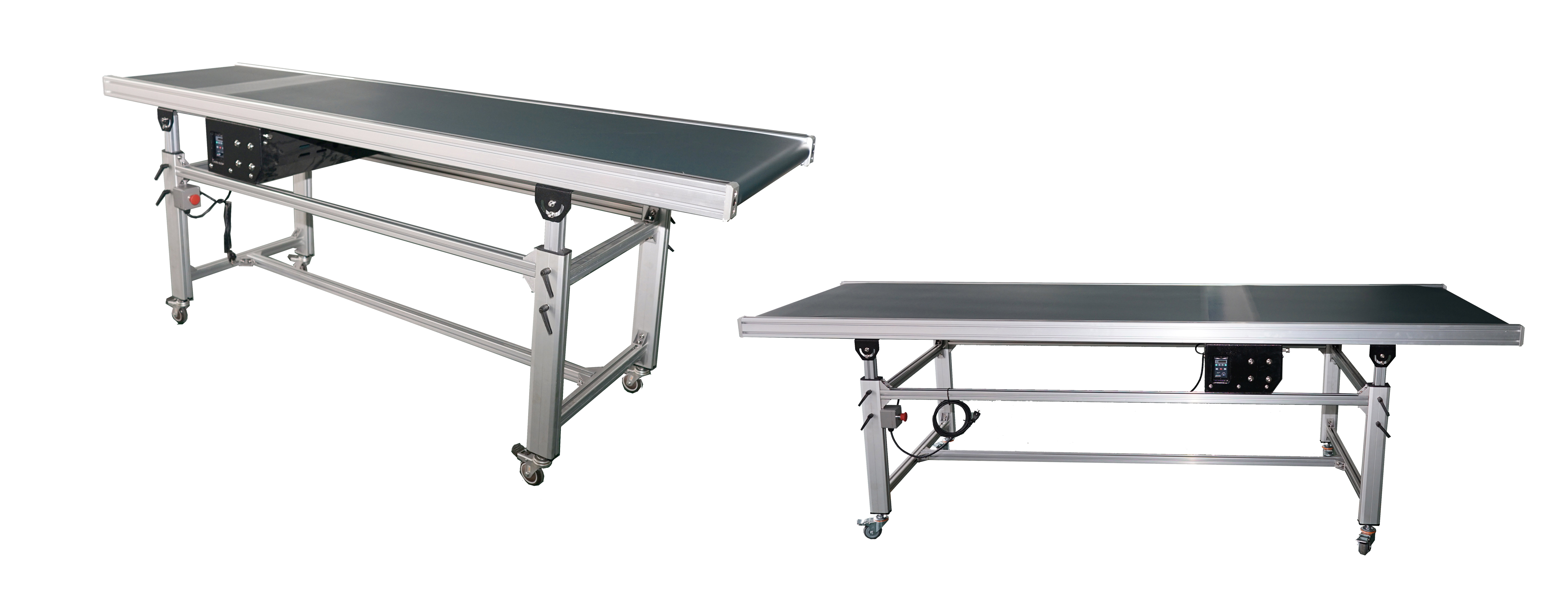
- Model
- Length/feet
- Belt width/in
- Width/in
- Height/in
- Speed
- Temperature
- Payload/Length
- Power
- Net weight/lbs
- 1236
- 12
- 36
- 38.78
- 32.5~44.75
- 0-9.84ft/m
- <176℉
- 6.71lbs/ft
- AC110V 120W
- 551
- 1036
- 10
- 36
- 38.78
- 32.5~44.75
- 0-9.84ft/m
- <176℉
- 6.71lbs/ft
- AC110V 120W
- 441
- 836
- 8
- 36
- 38.78
- 32.5~44.75
- 0-9.84ft/m
- <176℉
- 6.71lbs/ft
- AC110V 120W
- 331
- 1224
- 12
- 24
- 27
- 32.5~44.75
- 0-9.84ft/m
- <176℉
- 6.71lbs/ft
- AC110V 120W
- 419
- 1024
- 10
- 24
- 27
- 32.5~44.75
- 0-9.84ft/m
- <176℉
- 6.71lbs/ft
- AC110V 120W
- 353
- 824
- 8
- 24
- 27
- 32.5~44.75
- 0-9.84ft/m
- <176℉
- 6.71lbs/ft
- AC110V 120W
- 287
- 1220
- 12
- 20
- 23
- 32.5~44.75
- 0-9.84ft/m
- <176℉
- 6.71lbs/ft
- AC110V 120W
- 375
- 1020
- 10
- 20
- 23
- 32.5~44.75
- 0-9.84ft/m
- <176℉
- 6.71lbs/ft
- AC110V 120W
- 331
- 820
- 8
- 20
- 23
- 32.5~44.75
- 0-9.84ft/m
- <176℉
- 6.71lbs/ft
- AC110V 120W
- 287
Applications
- Low overhead take out
- Insert loading
- Labeling
- Part marking
- Assembling
- Inspection
- Palletizing
- Side by side Cobots
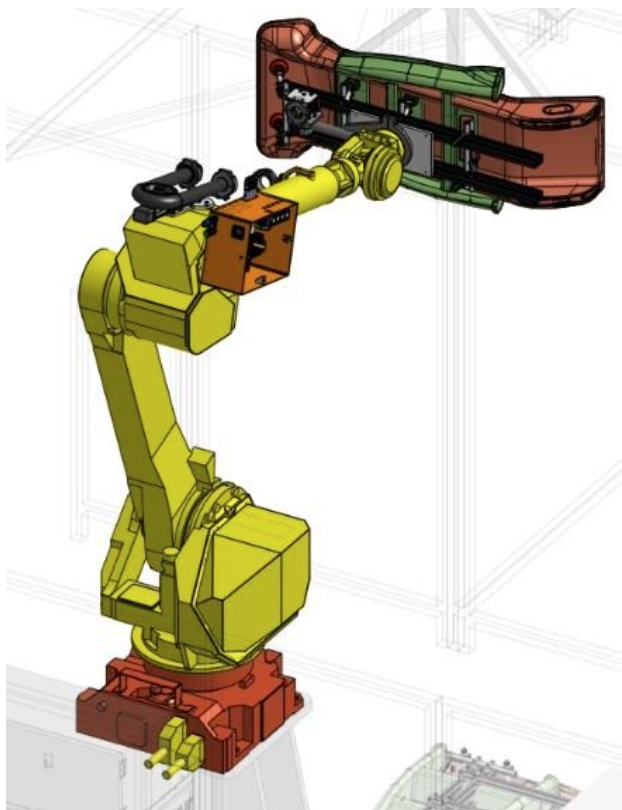
Available Fanuc Models
- M-710 | Large Tonnage Applications
- M-20 | Medium Tonnage Applications
- M-10 | Small Tonnage Applications
- CRX | Cobot (no guarding needed)
- SCARA | High-Speed Assembly
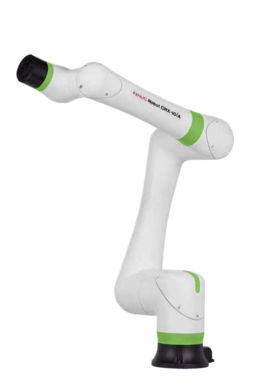
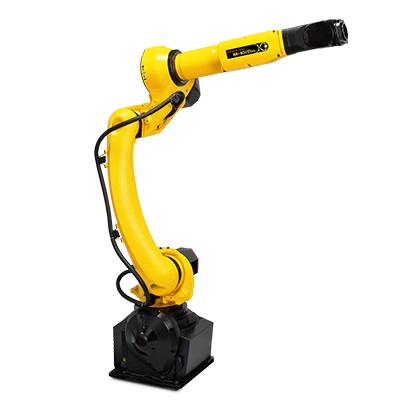
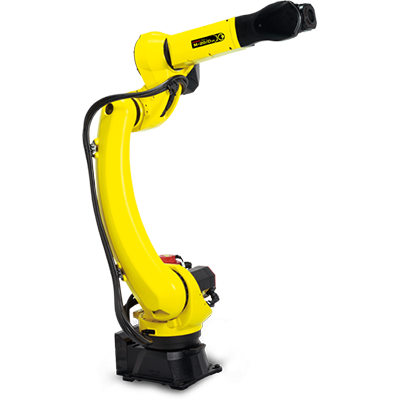
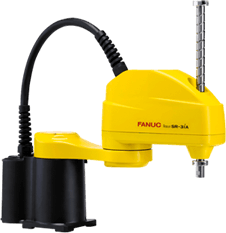
The Best Robot for Your Application
As the only plastics-industry focused automation integrator, we work across all FANUC robots including 6-Axis Robots, SCARA Robots, and CRX Cobots.
View Fanuc’s complete line of industrial robots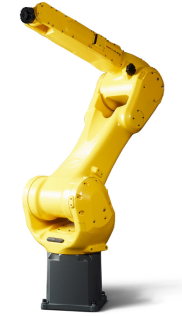
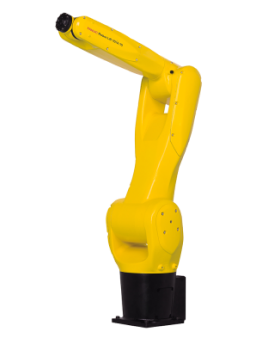
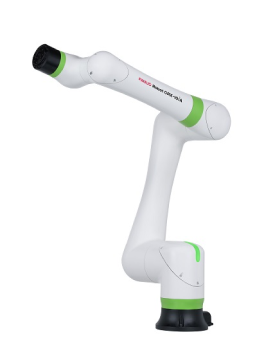
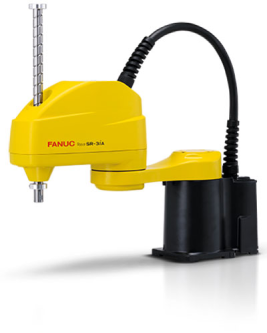
How We Work
Our in-house engineering team creates all end of arm tooling, and designs downstream automation.
We know what matters – We focus on delivering your system on time, on budget.
Collaboration is key – Successful automation projects require information exchange and accountability. We build a project plan and then do weekly project meetings to make sure any obstacles we encounter are quickly identified and addressed.
Transparency throughout – We share our proven process for executing projects and track progress with you each week. This process ensures there are no disconnects in scope or expectations.
All of our system integrator projects follow a process that we’ve carefully calibrated over the years. From simulations and 3D modelling, to factory acceptance testing, we ensure you achieve your target results.
We use the latest software tools for solid model design, simulation (ROBOGUIDE), and project management to streamline the startup process.
Robust customer support is the backbone of ARI. Our services include technical service (over the phone, through video conference, or on-site), documentation and training, and aftermarket parts supply.
Why Choose ARI?
As an established value-added distributor in the plastics industry, we understand the complexities that come along with automating your process. Through project quoting, engineering, and final project commissioning, we work side by side with owners, managers, engineers and operators.
Fast Delivery and Responsive Aftermarket Support
We know that uptime is critical to success in molding, which is why we stock parts and equipment in the US for quick delivery and installation. Our field service team is highly responsive and cross trained on our various product lines to provide optimum support round the clock.
Domain Expertise
As part of The Absolute Group of Companies, ARI is comprised of and surrounded by a team with extensive expertise in new and used injection molding machinery, automation, and auxiliary equipment.
Technical Depth
Our engineering and service teams use state of the art tools and resources to provide a detailed plan and solution for your projects. Standard automation projects are designed and reviewed extensively, 2D & 3D models of automation installs are created, and for the more complex and robust work cells, we have you covered. We work best when everyone is reading off the same sheet of music, and ARI makes sure to provide as much hands on support as possible to keep the project on time and on budget.
Documentation and Training
Detailed project documentation lets your team install, start-up, and troubleshoot your equipment with ease. Backed by extensive training resources ranging from on-site/online classes to our ARI Aftermarket Support Portal, parts and service are a phone call away.
Project Management
We make it easy for you to track project status with continued communication. Weekly project updates keep our team on schedule and on budget throughout the project’s lifetime. This way there are no surprises, and if there are any unexpected changes, we can quickly adapt.
Ongoing Support
Our aftermarket support team is always here for your troubleshooting questions, parts, and service needs. ARI has multiple US part stocking locations and an extensive field service engineer network across North America.
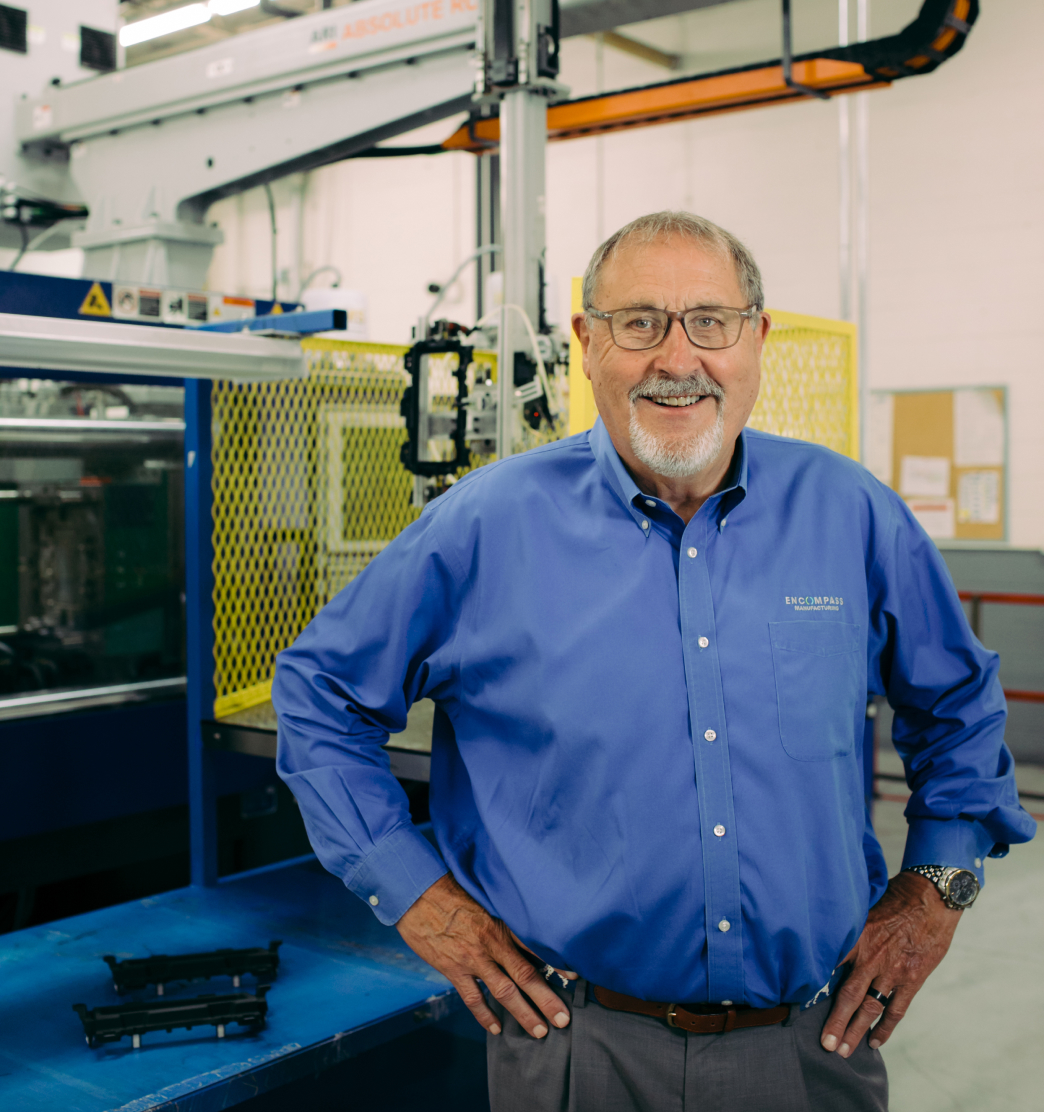
ARI is a valued partner consistently providing great products resulting in increased efficiency... the exceptional service they provide is a key factor in our success and growth.
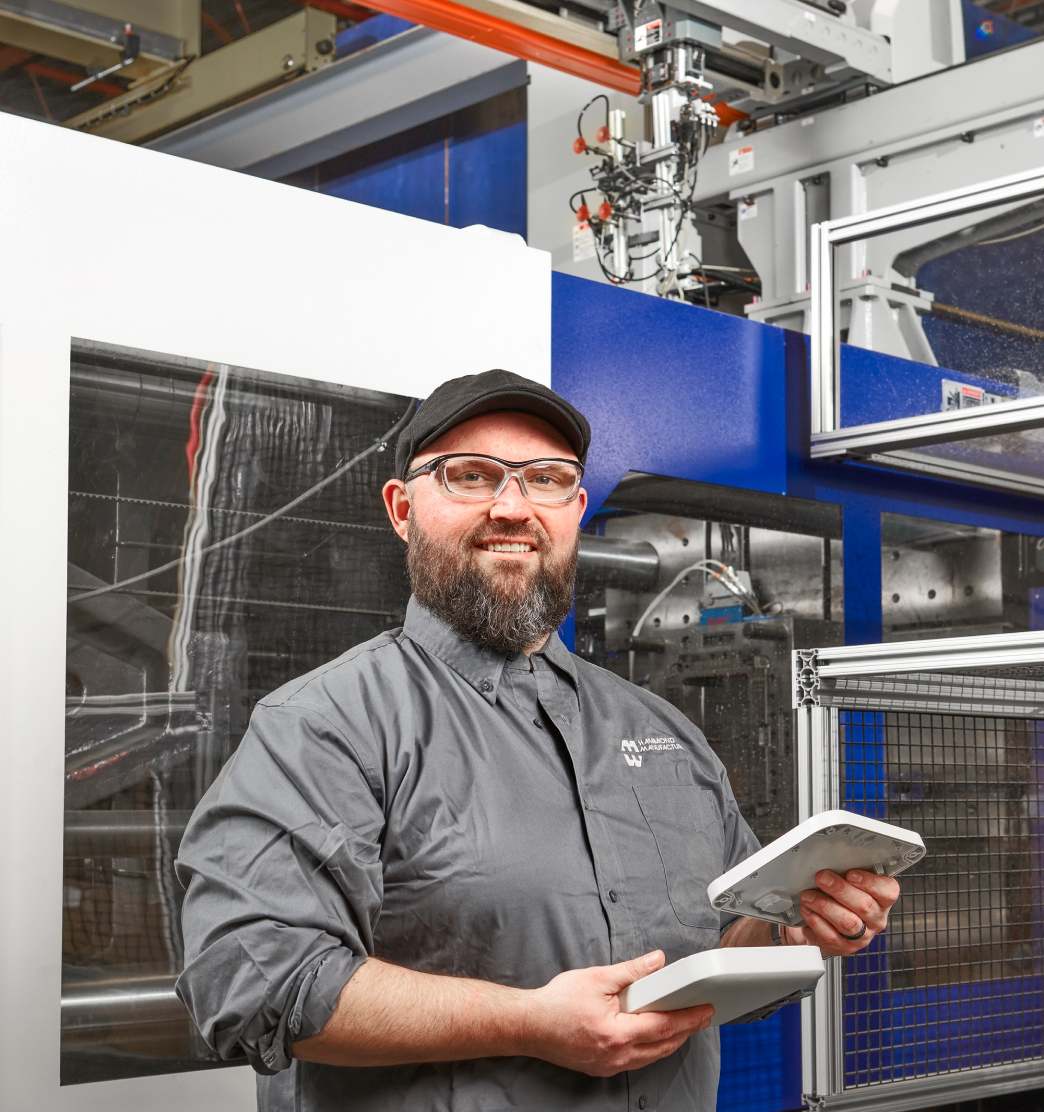
Automation has helped Hammond strengthen our competitiveness, improve our quality and achieve higher levels of profitability.