Choosing the right robot for your plastics manufacturing application: 3-, 5-, or 6-axis?
This guide helps you determine whether a 3-, 5-, or 6-axis robot is best for your plastics manufacturing needs, outlining key use cases and expert tips for optimal performance.
Selecting the right type of robot for your plastics manufacturing application can be challenging. The decision often comes down to whether a 3- or 5-axis top-entry robot will suffice or if a 6-axis robot is necessary. While there are exceptions to every rule, certain indicators can help guide your choice. This article delves into some of the “dead giveaways” that suggest which type of robot is best suited for your application.
3- and 5-Axis Robots: Ideal Scenarios
1. Pick and Place Applications
For simple pick-and-place tasks, a 3- or 5-axis robot is typically sufficient. These robots are excellent for handling variations in part stacking, specific drop sequences, or even degating. They can also manage more complex processes like insert molding in certain circumstances, showcasing general versatility.
3-axis robots are often chosen for their simplicity and cost-effectiveness. They operate by moving in three linear directions: X, Y, and Z. This makes them suitable for applications where parts need to be moved between fixed positions without the need for rotation or complex movements. For example, in a pick-and-place application where parts are picked from a conveyor belt and placed into packaging, a 3-axis robot can perform the task efficiently and reliably.
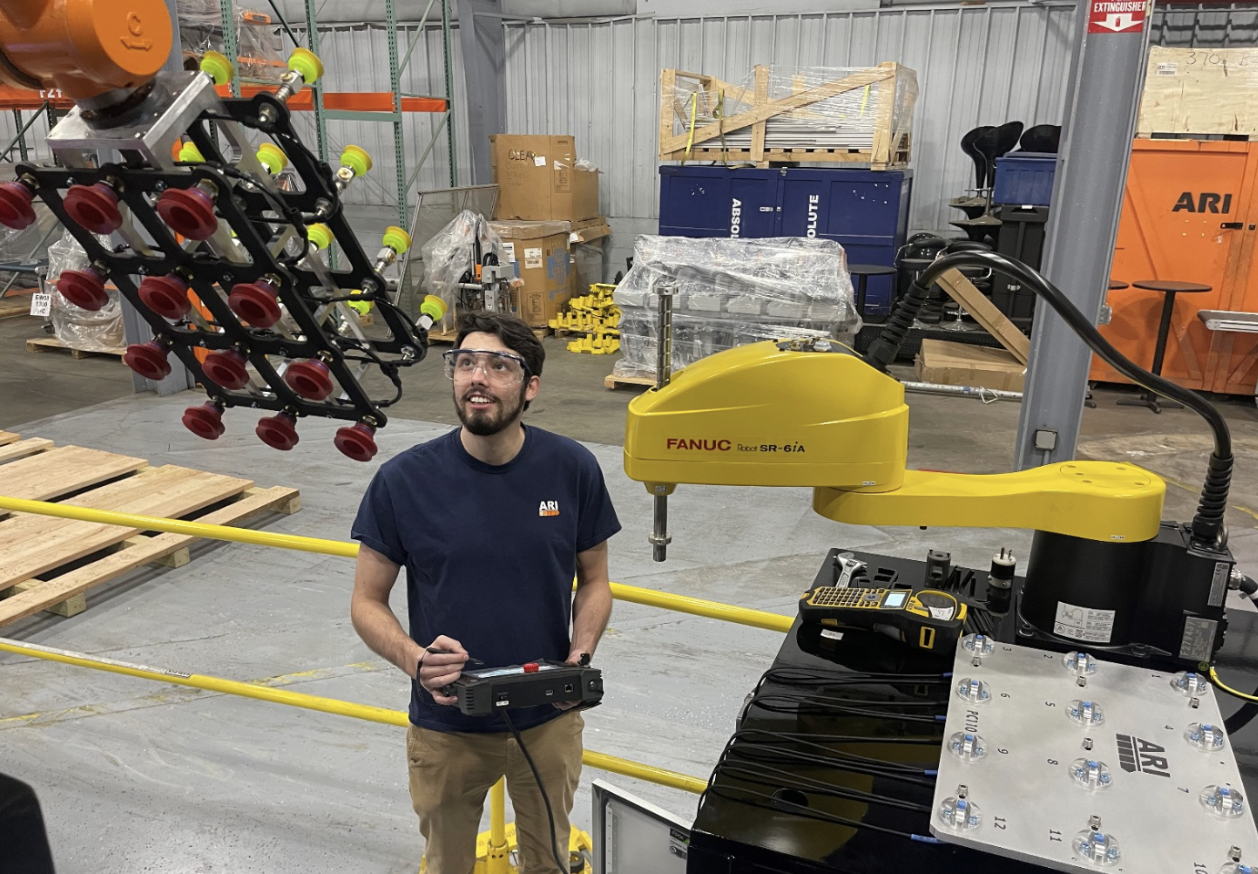
5-axis robots add two rotational movements to the three linear directions of a 3-axis robot, providing more flexibility and precision. This makes them ideal for tasks that require parts to be oriented in a specific way before placement. In applications involving part stacking or a specific drop sequence, the additional axes allow for better positioning and handling of parts, ensuring that they are placed accurately and consistently.
2. Fixed Orientation Tasks
In applications where parts need to be removed from a mold, the orientation of the parts typically remains the same throughout the process. A 3- or 5-axis robot can easily handle these tasks, as they do not require the ability to move and rotate the parts in multiple directions. This makes them well-suited for tasks such as loading and unloading parts from injection molding machines or CNC machines, where the parts are produced with a consistent process.
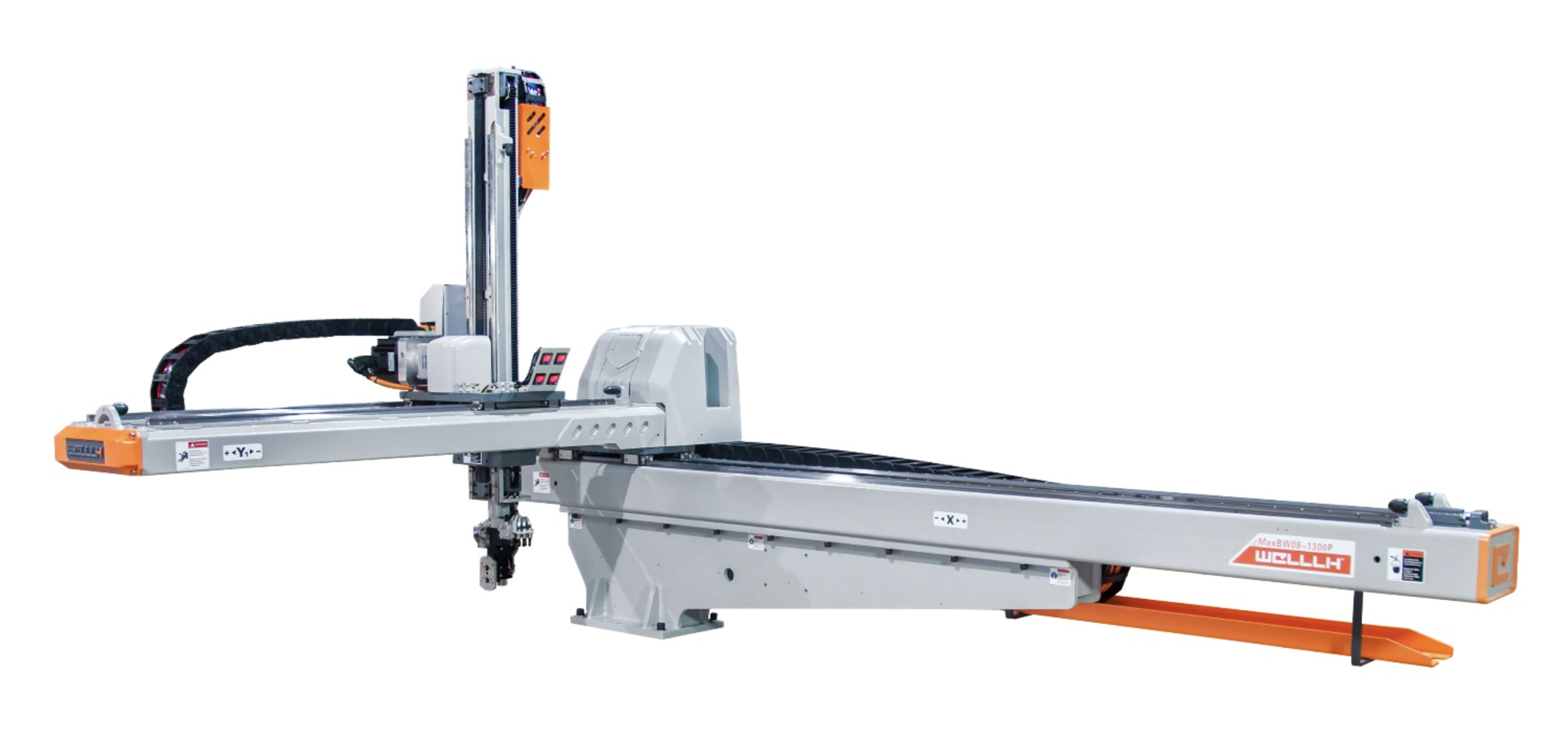
Another advantage of 3- and 5-axis robots is their ability to operate in a compact space. Their top-entry design allows them to be mounted directly above the work area, minimizing the footprint of the robotic system. This can be particularly beneficial in manufacturing environments where space is limited and maximizing floor space is crucial for general production efficiency.
6-Axis Robots: When to Consider
1. Downstream Automation
If your application involves downstream automation, a 6-axis robot is generally required. The maneuverability of a 6-axis articulating arm is essential for complex tasks such as assembly, welding or soldering, painting, machining, and intricate material removal. The flexibility and range of motion provided by a 6-axis robot make it indispensable in these contexts.
6-axis robots are capable of moving in six degrees of freedom: X, Y, Z, and three rotational axes. This allows them to perform complex movements and orientations that are not possible with 3- or 5-axis robots. For example, in assembly applications where parts need to be joined together in precise orientations, a 6-axis robot can easily handle the task by moving and rotating the parts into the required positions.
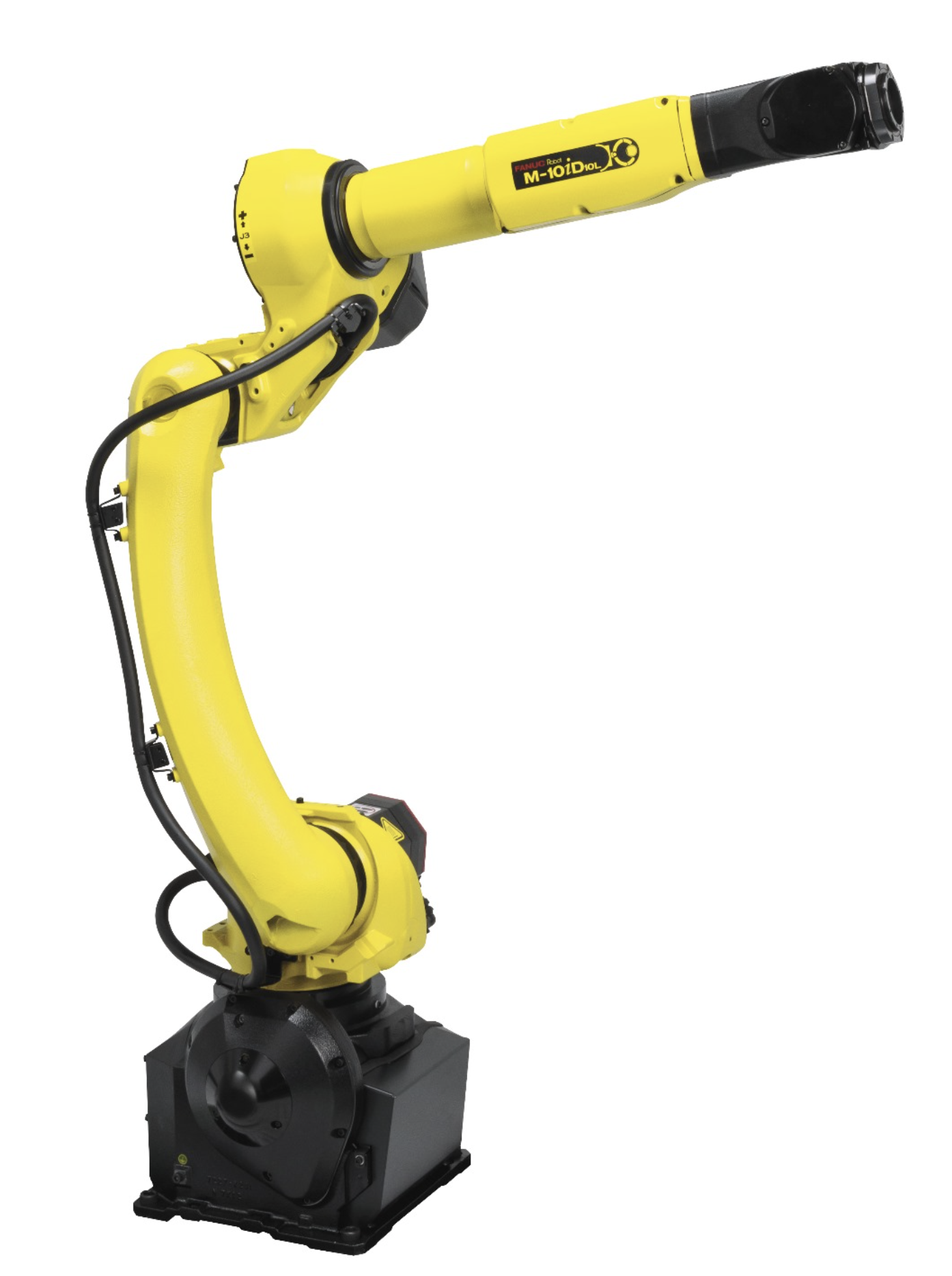
In welding and soldering applications, the ability to move the welding torch or soldering iron in multiple directions is essential for achieving high-quality welds and joints. A 6-axis robot can maneuver the tool into tight spaces and complex angles, ensuring that the welds are consistent and free of defects. Similarly, in painting applications, the flexibility of a 6-axis robot allows it to apply paint evenly and accurately to complex surfaces, resulting in a high-quality finish.
2. Complex Part Manipulation
Applications requiring complex manipulation are best served by a 6-axis robot. These robots can handle intricate movements and orientations that a 3- or 5-axis robot simply cannot achieve. Their advanced capabilities ensure that they can adapt to and perform complex tasks with precision.
For post-production manipulation of a part, a 6-axis robot can perform tasks such as drilling, milling, and grinding with high precision and repeatability. The ability to move the tool in multiple directions allows the robot to access hard-to-reach areas and perform intricate machining operations that would be difficult or impossible with a 3- or 5-axis robot.
Material removal applications, such as deburring and trimming, also benefit from the flexibility of a 6-axis robot. The robot can move the tool along complex paths and angles, ensuring that excess material is removed cleanly and accurately. This results in higher-quality parts with fewer defects and less rework.
Exceptions and Considerations
While the above indicators are useful guidelines, there are always exceptions. For instance, some customers might opt for a 6-axis robot when a more affordable 5-axis robot would suffice. Conversely, projects that overextend a 5-axis robot's capabilities might benefit significantly from a 6-axis robot.
Given these nuances, it is crucial to consult with an automation professional to map out all the specifics of your project. With over 1,250 robot installations in the US, and as a FANUC Authorized Systems Integrator (ASI) for 6-axis robotic applications, we have the expertise to help you determine the best robotic automation solution for your needs. Reach out to us if you're unsure which type of robot will best suit your project’s requirements.