World-Class Automation Integration
Looking to advance your automation strategy? As veterans of the plastics manufacturing industry, we provide a wide range of robotic automation solutions for molders, backed by signature aftermarket service.
Our Automation Solutions
3 & 5 Axis Top Entry Robots, 6 Axis Automation, Sprue Pickers, Conveyors, Guarding, Downstream Automation and Complete Machine Cells
Not sure what automation solution is right for you? Request a Quote
Latest Insights & Innovations
Explore fresh perspectives and breakthroughs handpicked by our team.
Our Automation Services
From sizing new robots to aftermarket parts and service, we support our customers through the whole lifecycle of their automation solutions.
Application Engineering
Our technical and organizational expertise ensures your project is engineered safely, efficiently and on-budget. From initial planning phase to post-installation support, our team of dedicated in-house engineers are there to assist at any point throughout your automation project.
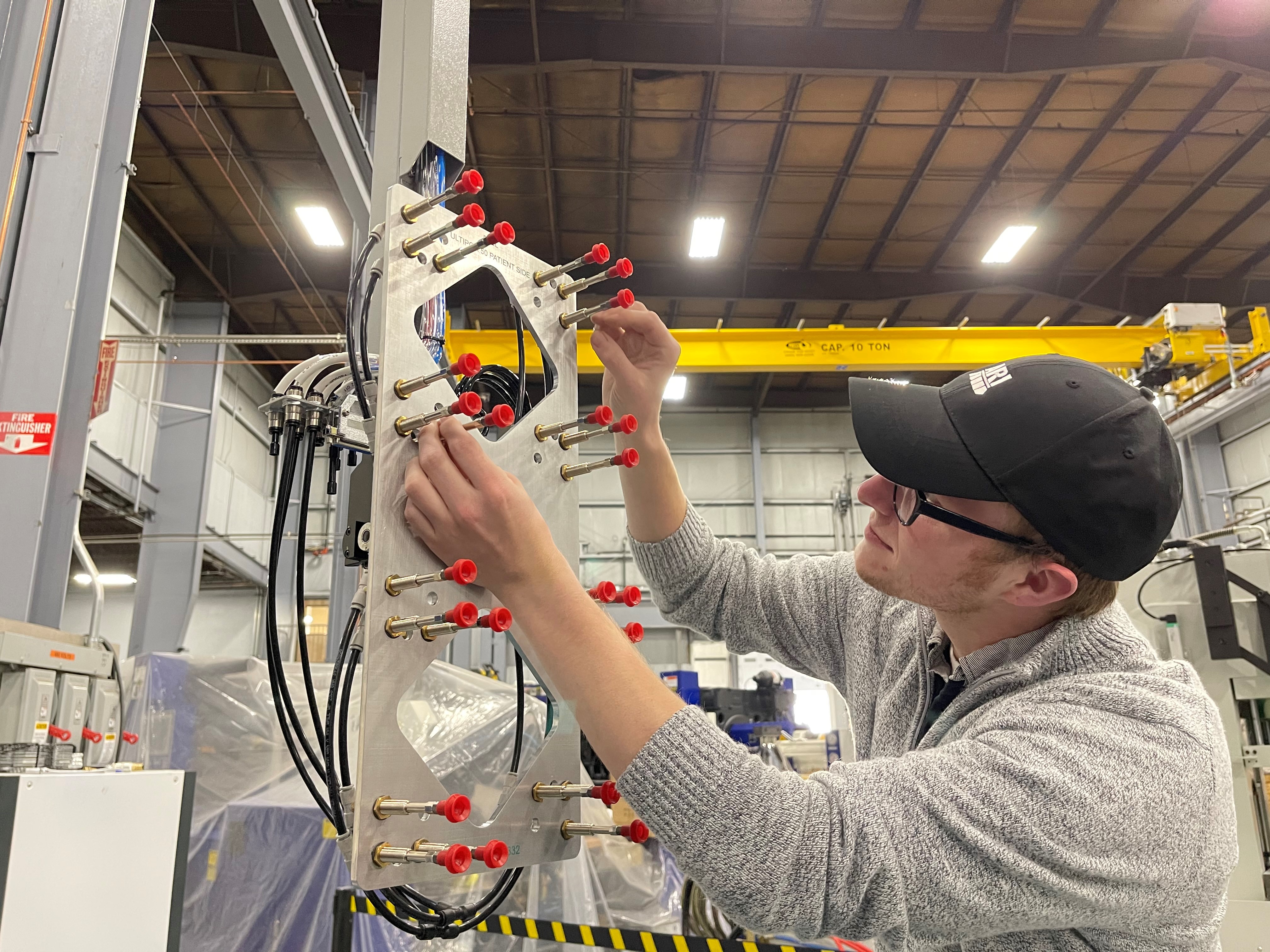
Aftermarket Support
ARI sources and stocks world-class components locally, ensuring low costs and quick lead time. Our aftermarket parts department is headquartered in Massachusetts with additional technical centers in Ohio and South Carolina. With full inventory of parts on US soil, lead time for replacement parts is never much longer than a day, and our customers can often source parts from local suppliers if necessary.
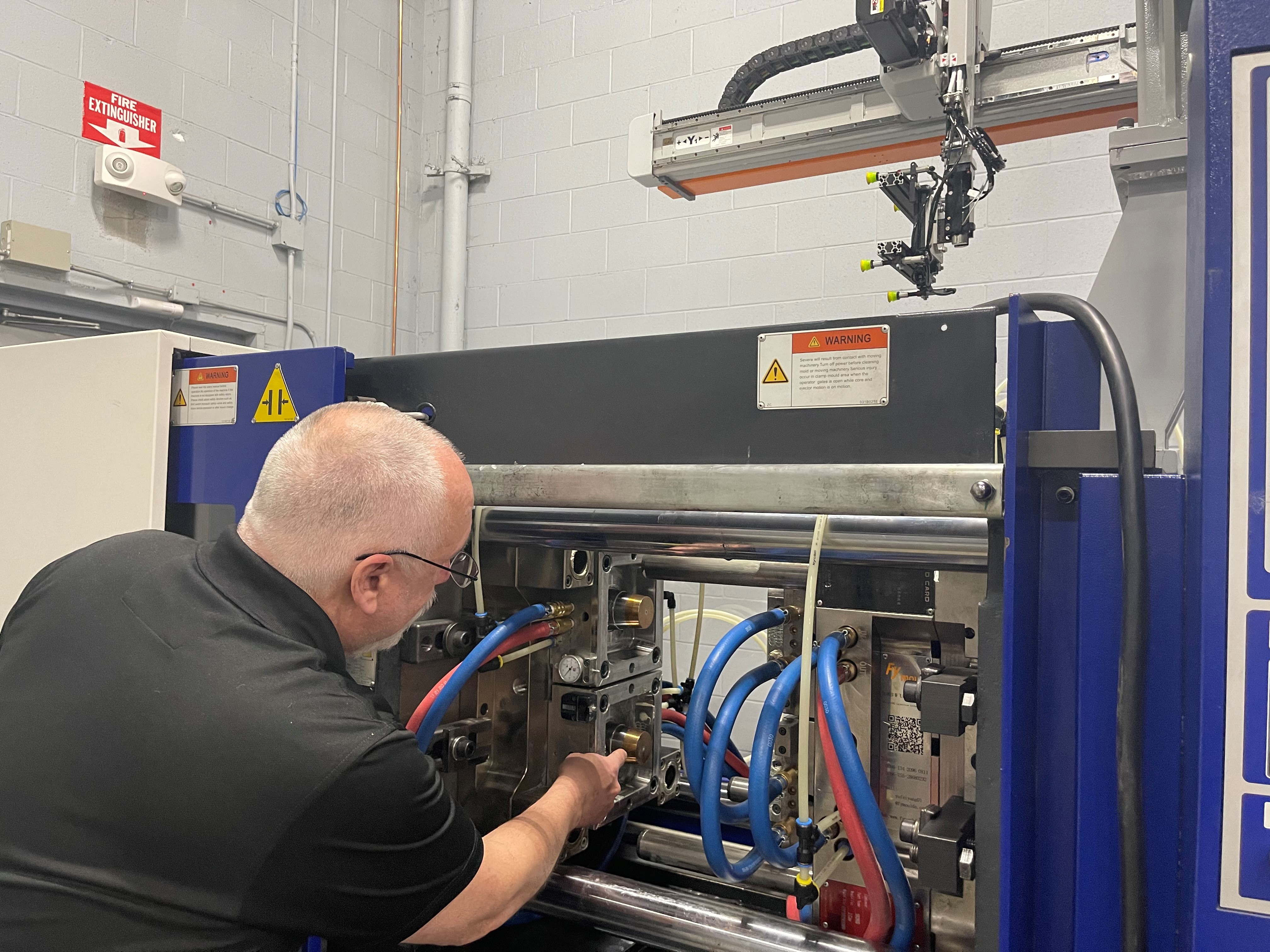
Training
Most customers opt for on site start up and training when they purchase a robot with ARI. In addition, we offer in person classes at our technical centers (MA, OH, & SC), and remote online training classes year-round. Check out the ARI Aftermarket Support Portal for detailed robot guides, troubleshooting videos and more!
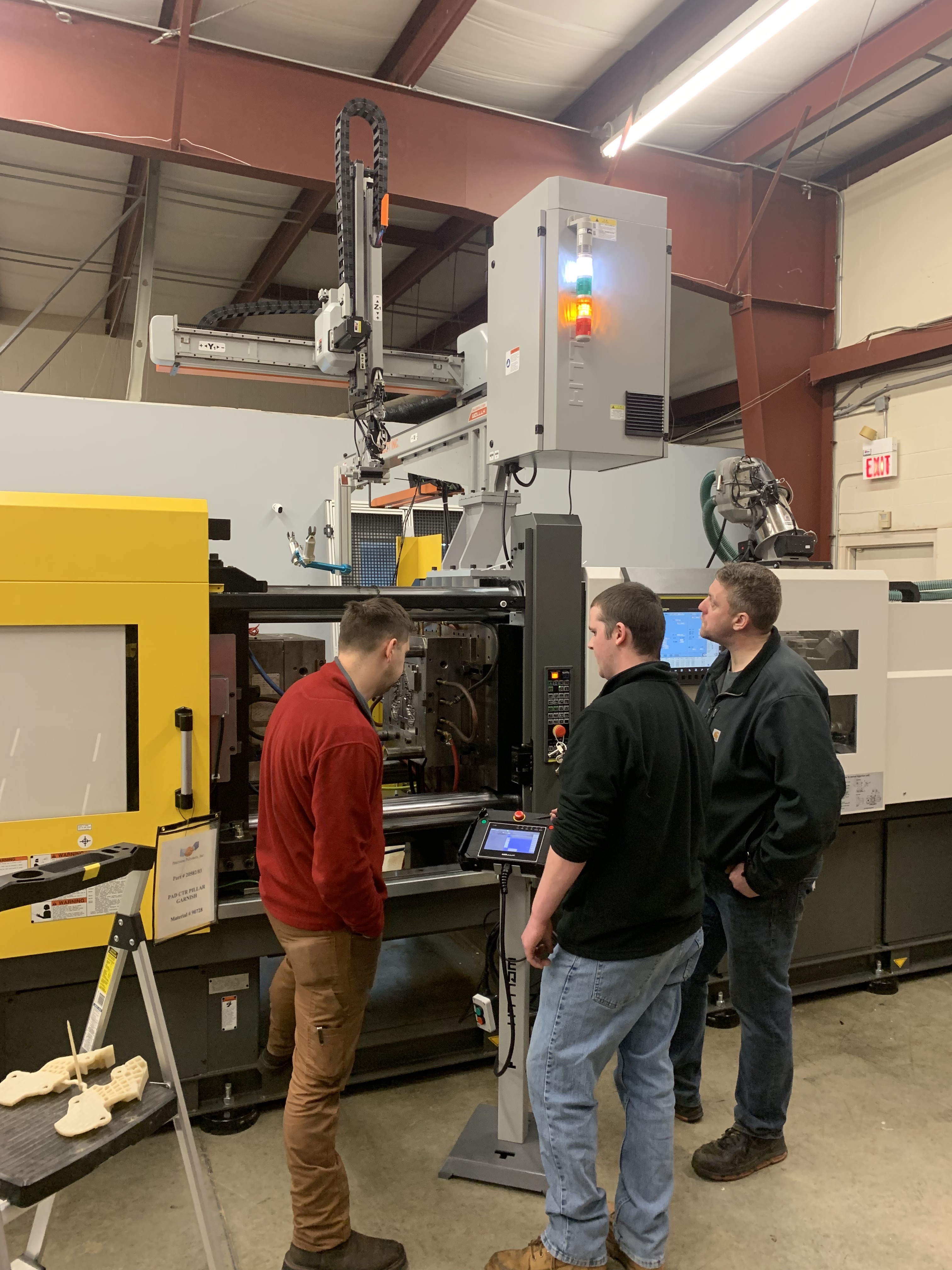
Have any questions about our services? Get in touch with us
Why Choose ARI?
As an established value-added distributor in the plastics industry, we understand the complexities that come along with automating your process. Through project quoting, engineering, and final project commissioning, we work side by side with owners, managers, engineers and operators.
Fast Delivery and Responsive Aftermarket Support
We know that uptime is critical to success in molding, which is why we stock parts and equipment in the US for quick delivery and installation. Our field service team is highly responsive and cross trained on our various product lines to provide optimum support round the clock.
Domain Expertise
As part of The Absolute Group of Companies, ARI is comprised of and surrounded by a team with extensive expertise in new and used injection molding machinery, automation, and auxiliary equipment.
Technical Depth
Our engineering and service teams use state of the art tools and resources to provide a detailed plan and solution for your projects. Standard automation projects are designed and reviewed extensively, 2D & 3D models of automation installs are created, and for the more complex and robust work cells, we have you covered. We work best when everyone is reading off the same sheet of music, and ARI makes sure to provide as much hands on support as possible to keep the project on time and on budget.
Documentation and Training
Detailed project documentation lets your team install, start-up, and troubleshoot your equipment with ease. Backed by extensive training resources ranging from on-site/online classes to our ARI Aftermarket Support Portal, parts and service are a phone call away.
Project Management
We make it easy for you to track project status with continued communication. Weekly project updates keep our team on schedule and on budget throughout the project’s lifetime. This way there are no surprises, and if there are any unexpected changes, we can quickly adapt.
Ongoing Support
Our aftermarket support team is always here for your troubleshooting questions, parts, and service needs. ARI has multiple US part stocking locations and an extensive field service engineer network across North America.
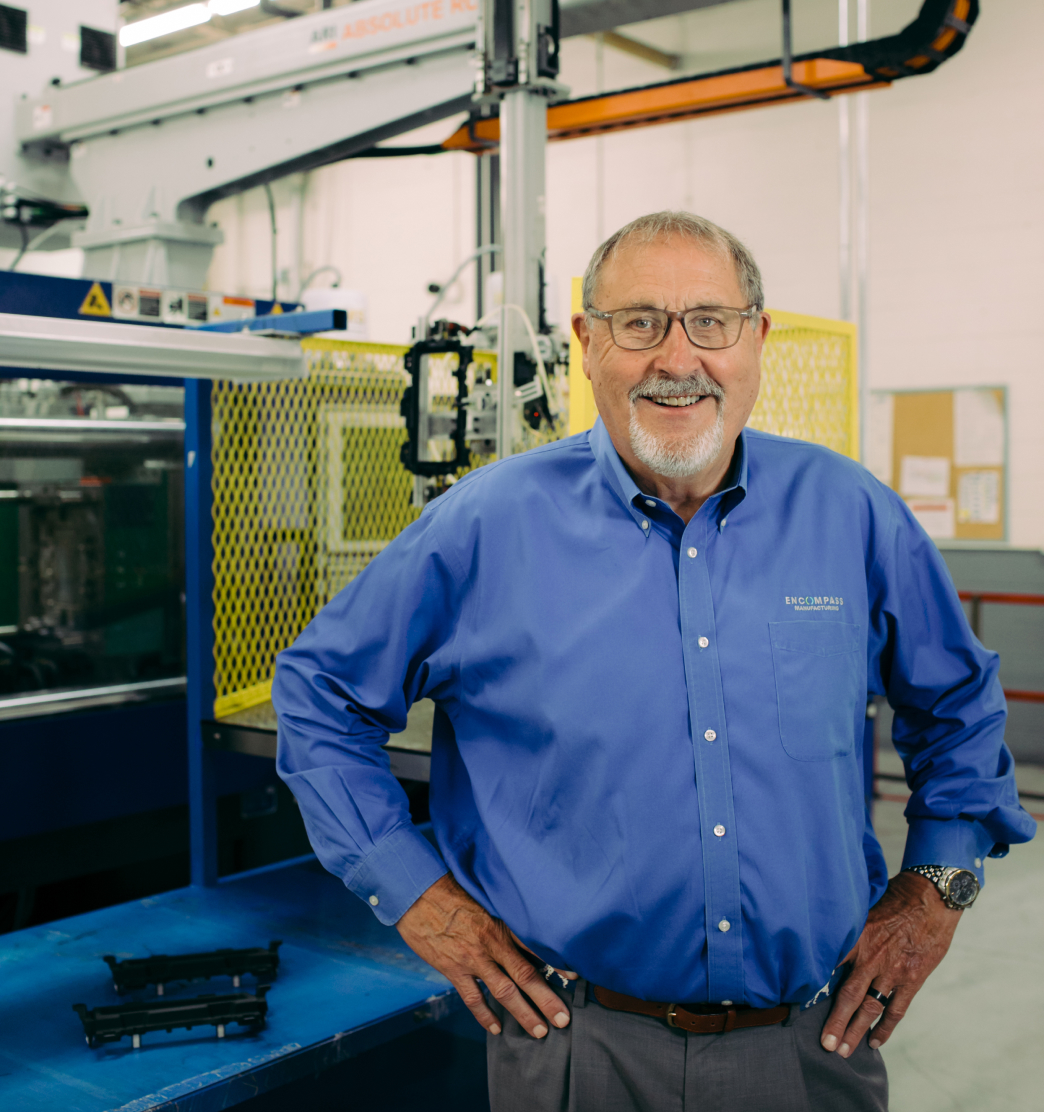
ARI is a valued partner consistently providing great products resulting in increased efficiency... the exceptional service they provide is a key factor in our success and growth.
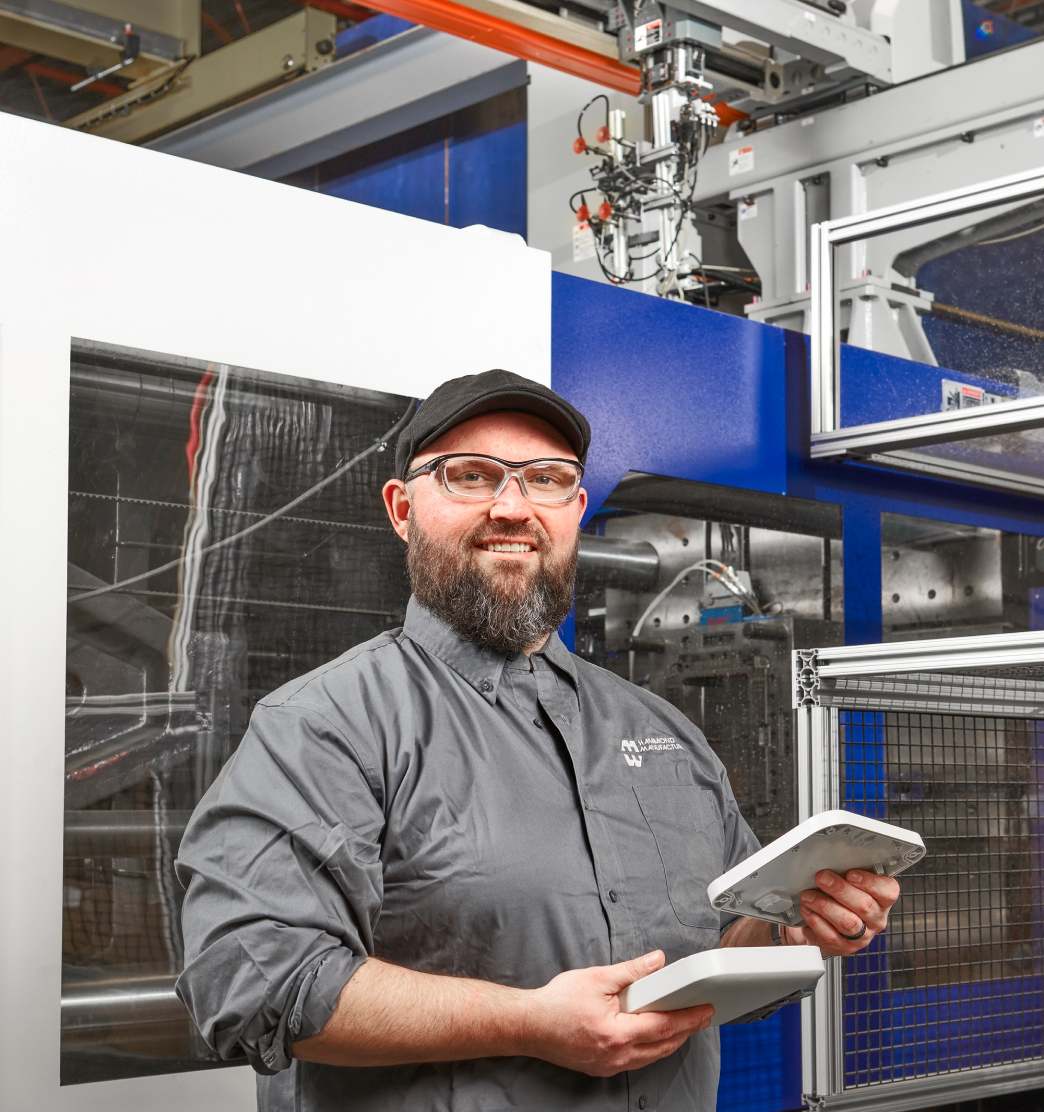
Automation has helped Hammond strengthen our competitiveness, improve our quality and achieve higher levels of profitability.